 |
 |
 |
 |
 |
 |
 |
 |
 |
 |
 |
 |
 |
 |
 |
 |
 |
 |
 |
 |
 |
 |
 |
 |
 |
 |
 |
 |
 |
 |
 |
 |
 |
 |
 |
 |
 |
 |
 |
 |
 |
 |
 |
 |
 |
 |
 |
 |
 |
 |
 |
 |
 |
 |
 |
 |
 |
 |
 |
 |
 |
 |
 |
 |
|
|
|
|
|
|
|
|
|
|
|
|
|
|
|
|
|
|
|
|
|
|
|
|
|
|
|
|
|
|
|
|
|
|
|
|
|
|
|
|
|
|
|
|
|
|
|
|
|
|
|
|
|
|
|
|
|
|
|
|
|
|
|
|
|
|
|
|
|
|
|
|
|
|
|
Boley (the proper name is G.Boley) were established in Germany in 1870 and went on to make a world-renowned range of precision machinery and equipment of all kinds - from miniature watchmakers' lathes of conventional WW and Geneva pattern (as well as triangular-bed and other unusual designs) medium-sized high-precision (include some complex and expensive types such as the fabulous 5LZ and simpler plain-turning 4BK), production units, various kinds of milling machines together with a vast range of watch and clock-making tools and accessories and precision drills. Even during the 1960s and 1970s their machine tools were still of the highest quality and included a number of remarkably advanced and sophisticated designs. Some G.Boley models were copied by Smart and Brown in England during WW2, the example most frequently found today being the Model M in Mk. 1 and Mk. 2 forms. Some confusion has arisen in recent years about the connection between G.Boley, Boley & Leinen and Leinen. Whilst Boley (G.Boley) were nothing to do with the other two, Leinen and Boley & Leinen were the same company and used two names as marketing tools. In general their smaller machines were "Boley & Leinen" and the larger, more sophisticated ones, "Leinen". A contact writes: The basic story, regarding the two Esslingen firms, I got either from Gunther Leinen, the grandson of the founder or from Fritz Carl Mahr, who was a good friend of Gunther's and the principal owner of the big measuring instrument firm of Carl Mahr. I also knew the son (Gunther's father) who was owner and manager of the firm at the end of the war - when, as an American Serviceman, I had my first contact with Boley and Leinen and with the firm of G.Boley. In any event, I was told that the manner by which Boley & Leinen acquired the Boley part of the name was a matter of acute embarrassment to the Leinen family. The founder of the firm, Gunther's grandfather, had been employed by G. Boley, and left them, initially, to manufacture the bench vise of his design. This vise was always marked "Leinen" even though it was always manufactured by Boley & Leinen. G. Boley also made an exact copy of this very popular item. My understanding is that Leinen was quite successful with the vise and decided to go into the watchmaker's lathe business; in direct competition with G. Boley; an already well-established name. Supposedly, he searched the town directory and located a not particularly well-off widow with the family name of Boley and persuaded her to become a "partner" in his firm. His firm thus became "Boley & Leinen". "G.Boley" lathes are still listed for sale today - but these are made in the Far East, and sometimes badged "Vector". A recent visit (2008) to the watchmakers' school in Furtwangen saw only Boley & Leinen WW-types in use, the teacher explaining that the older lathes were still employed because none of equal quality (in a WW-style) could be bought. A further disadvantage of the "Vector" is the very restricted accessory range (something a watchmaker really needs) - only the easily-made, less complex items being offered and with non of the original G.Boley and Boley & Leinen accessories fitting. After Boley & Leinen (but not G.Boley) closed, parts and complete WW-type lathes continued to be made for a time, though in very limited numbers, by redundant workers for two German distributors, Prätecma and Precima. If any reader has a Boley lathe that they would like to see it featured in the Archive, the writer would be interested to hear from you..
|
|
|
|
|
|
|
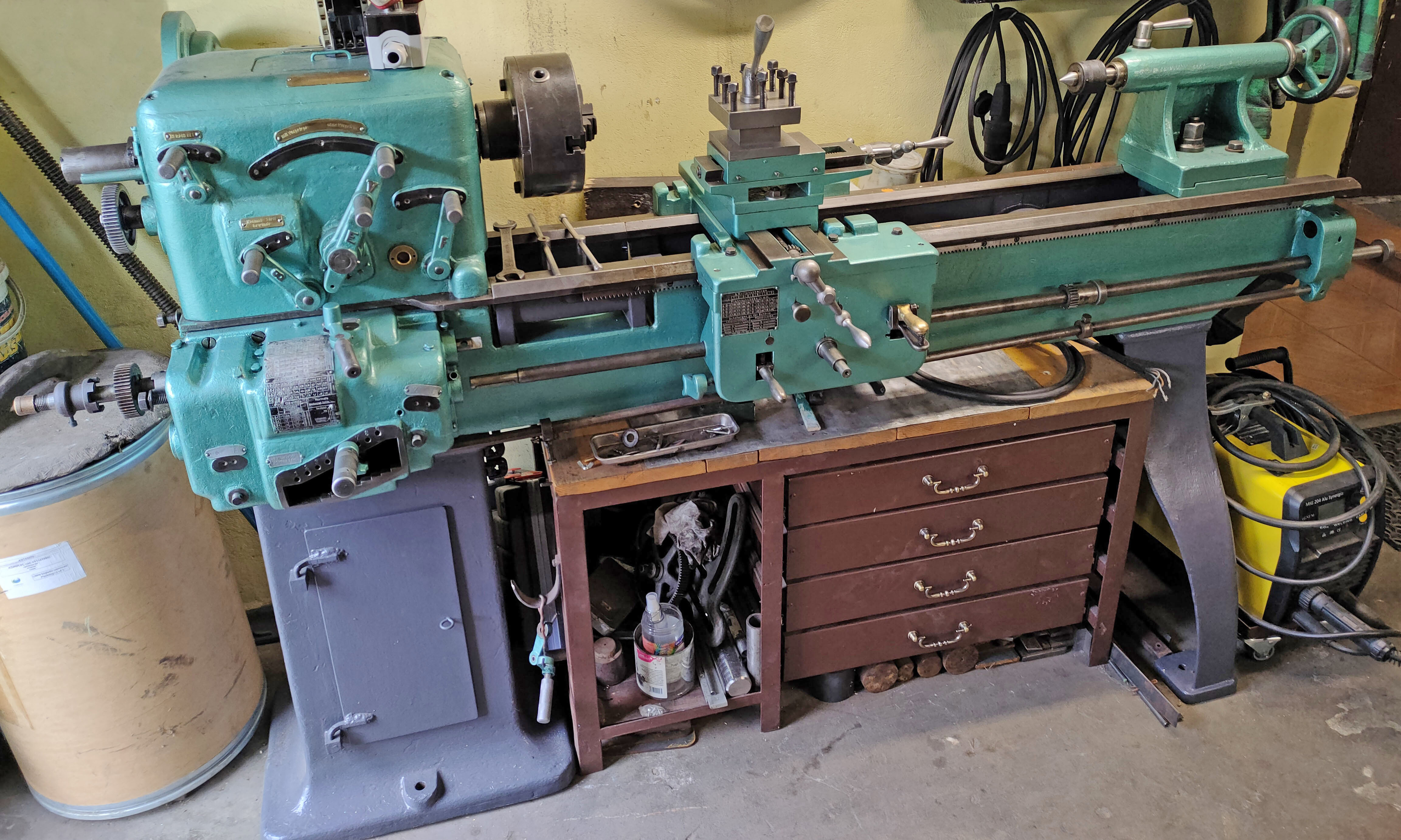 |
|
|
|
|
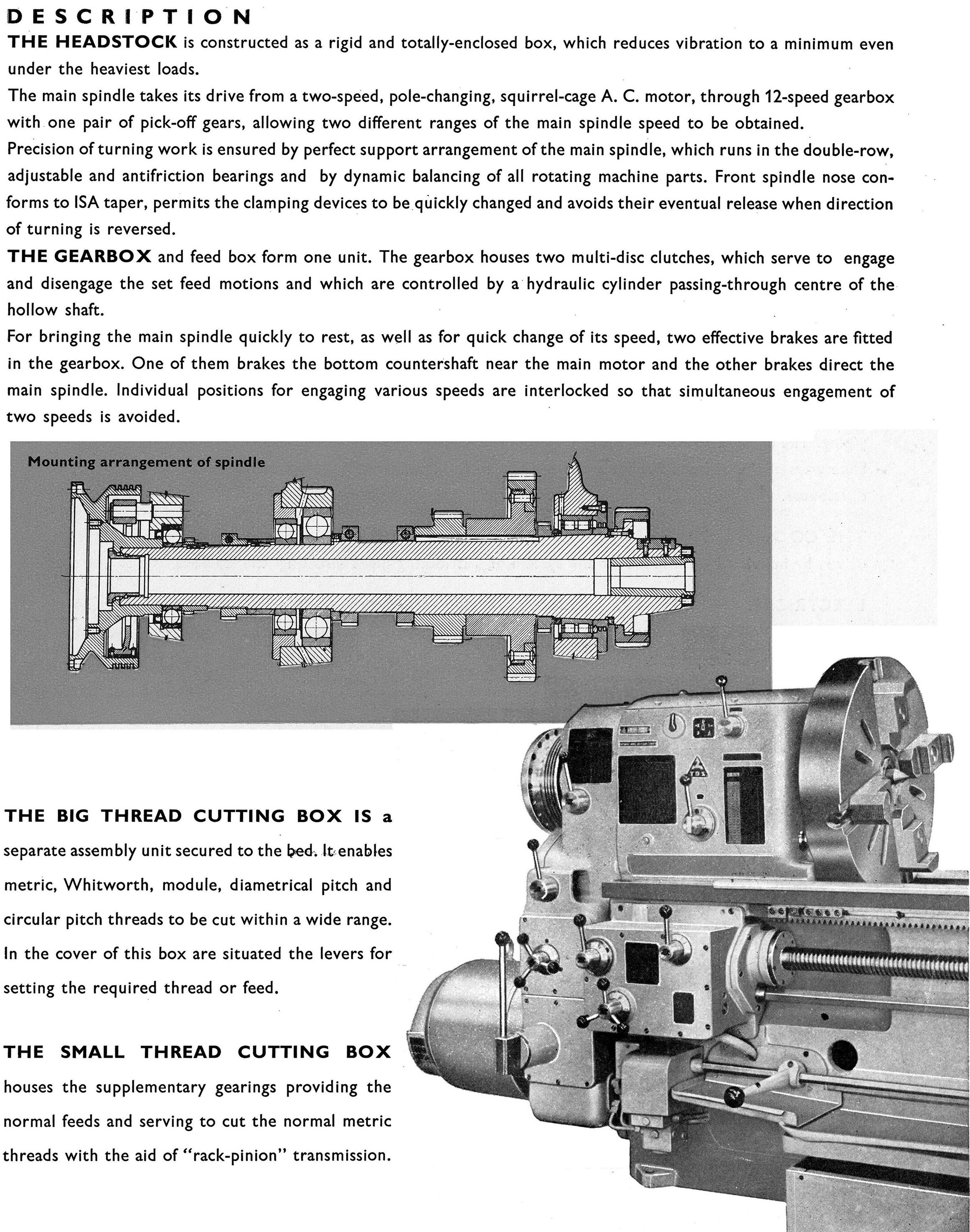 |
|
|
|
|
The works of G.Boley and Company in 1924
|
|
|
|
|
|
|
 |
|
|
|
|
|
|
|
|
|
|
|
One of G.Boley's most popular and enduring models was built as the Series 3 and 4 - both very similar in construction but with the No. 3 lathe being of 90 mm (3.5") centre height and the No. 4 120 mm (4.7"). Illustrated below (with a photographic essay here of the later, more highly-developed models) these were enormously heavy, cleverly designed, beautifully made and elegant machine tools produced in a wide variety of models and with suffixes such as L, C, L, H, R, CR, BJ, HL, HM, etc. - the designation reflecting a precise specification and level of standard equipment. Production began in the early 1920s - as a plain-turning model with an open-drive headstock and a variety of countershafts for bench or stand mounting drive - and extended to at least the mid 1970s by which time, in backgeared and screwcutting form, it was fitted to a very heavy cast-iron self-contained stand with built-in motor drive. While many 3L and 4L models were produced as plain-turning precision lathes, or set up with lever-action collet closers, capstan heads and cut-off slides for mass-production and second-operation work on small, close-tolerance components used in the watch, clock and instrument industries, large numbers were also manufactured, from the late 1920s, as backgeared and screwcutting models for use in toolrooms and repair shops. On the latter type the leadscrew ran in a fully-shielded housing beneath the bed while the twin "aprons" (they reached down both in front of and behind the saddle to form a particularly rigid housing) were joined together by a casting that supported the clasp nut in a perfect position directly beneath the centre line of the carriage and almost underneath the toolpost. Neatly enclosed within the headstock casting directly behind the chuck the backgear and its engagement system (when fitted) was a masterpiece of compact engineering, if a little awkward to engage on early versions--and a complete mystery if you don't know how. The secret lies in a small pressed-steel lever on the face of the headstock beneath the chuck (used to engage and disengage the gears) and a difficult-to-locate small screw marked (in tiny lettering) "AUS" and "EIN" (in and out) on the side step of the middle pulley. If the screw is turned through 180 degrees, whilst simultaneously oscillating the pulley, a slight "clunk" will be heard as a small spring-loaded pin engages (or disengages) the pulley from the inner (bronze) backgear. With the pin out of engagement the pulley is free to turn on the spindle (together with its gear) and so engage the backgear assembly to give slow speeds. The pushing force for the pulley-to-gear engagement pin was provided by a powerful spring, contained in a housing bored down through the depth of the largest diameter pulley. The tapping was capped by a large, slot-head screw that should be removed only if necessary - and if it is be sure to cap the assembly with a rag to contain the bits as they attempt to fly out. The saddle drive was fitted with an automatic, pre-set disengage to both left and right travel - a most useful facility when taking a long, fine-finishing cut. On some versions of this lathe the headstock pulley ran in its own bearings (concentric to the main spindle bearings) and drove the spindle though a peg - thus relieving the spindle of any loads from the driving belt. The "tumble-reverse" mechanism (to reverse the direction of the carriage feed) was unusual (and very economically engineered) in that the whole of the banjo arm carrying the changewheels was swung through an arc to pick up the respective drive gear. A knurled-finished handle below the left-hand headstock bearing operated the mechanism. The lathe was available in several other short-bed versions - the H, a simple repetition lathe, the PA for polishing, PS for finishing and the G for finishing and re-cutting threads. Several different stands were available, all of simple design with cast-iron legs and either wooden or metal tops. Models from the mid 1930s were offered with the option of a neat under-drive cast-iron stand with the flat-belt final drive coming from a V-belt countershaft unit built into the lower part of the headstock-end leg (illustrated below). The plain turning precision lathes used a very much simpler form of bed than the screwcutting models, although parts of the compound slide and tailstock - as well as a number of accessories - were common to all types and could be easily interchanged. One example of the 3 Series - it might be unique - has been found with a spindle clutch Although the G.Boley company no longer exists their machine tools remain in widespread use through industry, especially in repair shops. A typical example is the Swiss Rhaetische Bahn's locomotive shops at Landquart where a number of late-production, larger Boley machines, including a CNC affair, are in full-time use. Boley vices are everywhere in the spotless shop and, once a year they have a TdOT or open-house day (in case you are ever in the country at the time). RhB manufactures all the parts need to keep their narrow-gauge (1m) engines and rolling stock in perfect working order. Some G.Boley models, both precision pain turning and screwcutting, were re-badged using the name "Swisten" for distribution in the UK while other were copied and sold as the Excel..
|
|
|
|
|
|
|
 |
|
|
|
|
|
Boley Model 3L/4L precision screwcutting and backgeared lathe as first manufactured in the 1920s (photographs here). Tumble reverse was operated by rocking the whole of the changewheel quadrant arm. In later years the 4L was made even more rugged and useful by boxing in the headstock casting to improve its rigidity, modifying the bed, extending the saddle wings forwards and mounting the lathe on a very heavy stand with an underdrive countershaft. Many of the other Boley lathes shown below, the 3C, 3R, 4R, 3BJ, 3H, 3HK, 3HL and 3HM were also gradually improved and strengthened during the 1930s and 1940s. The Boley 4L formed the basis for the post-war English Smart & Brown Model M
|
|
|
|
|
|
|
|
|
|
 |
|
|
|
|
|
|
Plain-turning Boley 3C (90 mm centre height) and 4C (120 mm centre height) with draw-tube collet closer and screw-feed compound slide rest. Theses were the simplest of the Boley 3 & 4 series and supplied for either bench mounting, or on choice of several different stands. One alteration incorporated when the lathe was to be mounted on an underdrive stand was to guard the drive belt by bolting a cast-iron plate to the front face of the headstock - the plate proving to be an ideal place on which to mount the insignia of a distributor or dealer.
|
|
|
|
|
|
|
 |
|
|
|
|
|
|
Boley lathe No. 3R and 4R. Almost identical to the No. 3 and No. 4 but fitted with a hardened-steel and phosphor-bronze back-gear assembly to give a range of slow speeds.
|
|
|
|
|
|
|
|
|
|
 |
|
|
|
Boley 2HN lathe with lever-operated collet closer and an unusual 6-position turret head on the hand-like tool rest.
|
|
|
|
|
|
|
|
|
|
|
|
 |
|
|
|
|
|
|
Plain-turning Boley 3BJ lathe with lever-action collet closer and a standard compound slide rest
|
|
|
|
|
|
|
 |
|
|
|
|
|
|
Boley 3H with all lever-action controls: collet closer slide rests and a tailstock with an indexing multi-tool holder
|
|
|
|
|
|
|
 |
|
|
|
|
|
|
Boley 3HK--similar to the 3H but with an ordinary screw-feed tailstock
|
|
|
|
|
|
|
|
|
|
|
|
 |
|
|
|
|
|
|
Boley 3HL: lever-action collet closer and collet-holding tailstock with a screw-feed compound slide rest
|
|
|
|
|
|
|
 |
|
|
|
|
|
|
Boley 3HM: an all lever-feed model for production work
|
|
|
|
|
|
|
 |
|
|
|
|
|
|
Boley 4PP thread-chasing lathe
|
|
|
|
|
|
|
|
|
|
|
|
 |
|
|
|
|
|
|
Boley 4PQ precision finishing lathe with thread-chasing attachment
|
|
|
|
|
|
|
 |
|
|
|
|
|
|
Boley PS lathe for short, collet-held repetition work
|
|
|
|
|
|
|
 |
|
|
|
|
|
|
Boley Model G tapping lathe. The two headstock pulleys were driven by belts running in opposite directions. A dog clutch, set between the pulleys, was arranged to flick from one drive to the other, so reversing the tap at high speed. Many users used ingenious adaptations to this design including automatic operation of the clutch controlled by mercury switches.
|
|
|
|
|
|
|
 |
|
|
|
|
|
|
|
Boley PA polishing lathe--though its actual use was for hand-turning or the finishing of small parts - the foot-operated collet closer allowing the operator to rack up a good bonus if he had taken tap-dancing lessons.
|
|
|
|
|
|
|
|
|
|
|
|
|
|
|
|
 |
|
|
|
|
|
|
Boley 3L from 1925 complete with the now seldom-found "overhead"
|
|
|
|
|
|
|
 |
|
|
|
|
 |
|
|
|
|
|
|
|
|
 |
|
|
|
 |
|
|
|
 |
|
|
|
|
 |
|
|
|
|
|
|
|
|
|
 |
|
|
|
|
Spindle and bearings from the headstock of the 1925 Boley 3L Backgear was arranged in a manner not dissimilar to that employed on many much cheaper lathes such as the Myford ML2, ML7 and ML10, with the gearing clustered together just inboard of the front spindle bearing - the lower pair of gears being carried on an eccentric shaft below the spindle line. The flat-belt drive pulley was fitted with an inserted bronze gear and could be locked and unlocked to a large "bull gear" keyed to the spindle. However, on the Boley, the details of the mechanism were very much more sophisticated with a spring applying a load to the long, square-headed joining bolt that passed through the whole assembly. Although the mechanism was quick and easy to lock and unlock, the force applied was sufficient to eliminate any play between the parts, an angled flange enabling a snug-fitting joint to be achieved.
|
|
|
|
|
|
|
|
|
 |
|
|
|
|
|
|
Above and below: spindle and assembled bearings from the 1925 Boley 3L
|
|
|
|
|
|
|
 |
|
|
|
|
|
|
|
|
|
 |
|
|
|
|
 |
|
|
|
|
 |
|
|
|
|
|
|
|
|
|
 |
|
|
|
|
 |
|
|
|
|
|
|
|
|
|