 |
 |
 |
 |
 |
 |
 |
 |
 |
 |
 |
 |
 |
 |
 |
 |
 |
 |
 |
 |
 |
 |
 |
 |
|
|
|
|
|
|
|
|
|
|
|
|
|
|
|
|
|
|
|
|
|
|
|
|
|
|
|
E-Mail Tony@lathes.co.uk Home Machine Tool Archive Machine Tools For Sale & Wanted Machine Tool Manuals Catalogues Belts Books Accessories
Benson Miniature Milling Machine
Benson Miller Page 2 Benson Home Page
A Benson lathe catalogue is available
Virtually unknown - pointing to the fact that few can have been made - the Benson milling machine would have been current during the 1930s, one example carrying a brass plate inscribed: Air Ministry Contract No 66794/37CX11 with the year of manufacture stated as 1938 and the serial number 843. Well made, in typical Benson fashion, the miller was a simple, horizontal type that lacked the provision to carry an overarm and drop bracket to support a full-length arbor - its use being confined to stub-mounted cutters. Unlike similar models from American makers of small precision machine tools, for example, Ames, Cataract/Hardinge and Rivett, it more resembled the Carter & Hakes in having a narrow, one-piece body and integral foot with an elevating knee and compound table assembly. 18" x 47/8" the table had two bevelled-edged T-slots and a single traverse T-slot off-set from the centre line - the latter possibly intended to mount the maker's dividing attachment. Both the longitudinal and traverse feed screws were 0.625" x 10 t.p.i., the lengthwise travel was 10.5", the screw passing through a bronze nut split and adjustable to eliminate backlash. The 3.5" of cross travel was provided by a very large-diameter, finely threaded boss that meshed with a rack - in the same manner as employed on some Pre-WW-2 Mikron precision milling machines. Elevation of the knee through its 6.5" of travel was through right-angle drive helical gears and a vertical screw, this arrangement giving a smoother, more controllable feed than the ordinary bevel-gears and screw (or the simple lever-lift type) sometimes found on this class of machine. High-quality, finely-engraved zeroing micrometer dials were fitted to each axis, their faces having a slight bevel and with locking by knurled-edge, face-thrust screws - the design ensuring that the setting was not lost as the lock was applied. As the machine was limited to basic work with a stub cutter, the intention may have been to supply a machine that could be tooled as part of a production process or used along aside more complicated models for simple jobs. However, far from being a simple machine, it reflected the Benson Company's obsession with quality, having a spindle with a double-step taper at the front (shallow to take radial loads and steep to take axial thrust) and both a threaded nose and a ground taper to accept draw-tube retained collets. Bearings were a shallow angle, tapered white-metal type at the front and, at the rear, a parallel-bore in bronze with a tapered outside with a bronze retaining/adjusting nut screwed to its end face. Inboard of the front bearing the spindle had what appears to have been a ground-in thread (8 t.p.i. x 1.625 o/d) that drew the spindle into its bearing housing to set the end thrust against the steep taper ground into the outside face of the bore. If you have a Benson miller, the writer would be interested to hear from you, With thanks to Mr Neil Partington for taking the time and trouble to submit the photographs below of a refurbished machine..
|
|
|
|
|
|
|
|
|
|
|
|
|
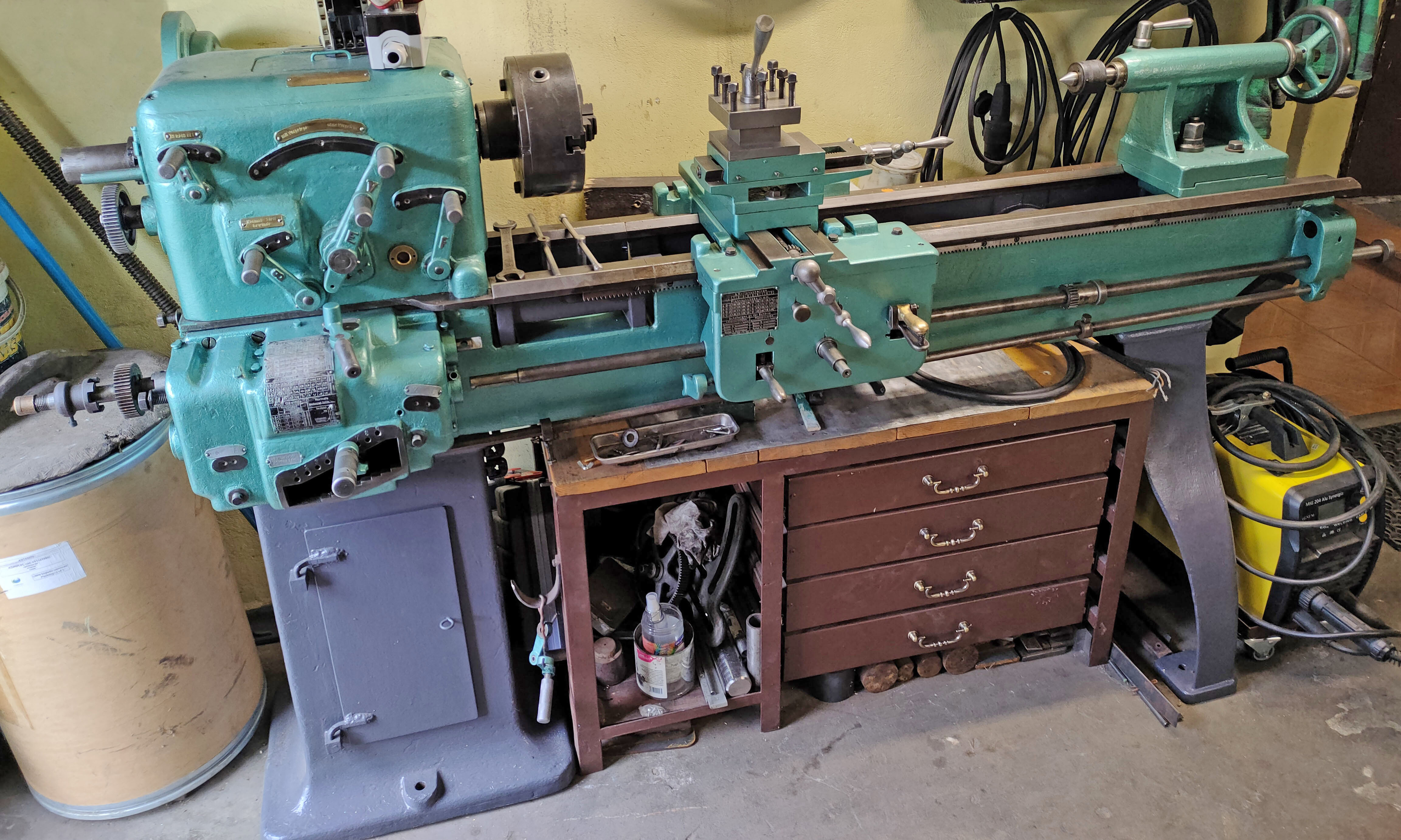 |
|
|
|
|
|
|
|
|
|
Benson precision miniature milling machine - converted from flat-belt to V-belt drive
|
|
|
|
|
|
|
|
|
|
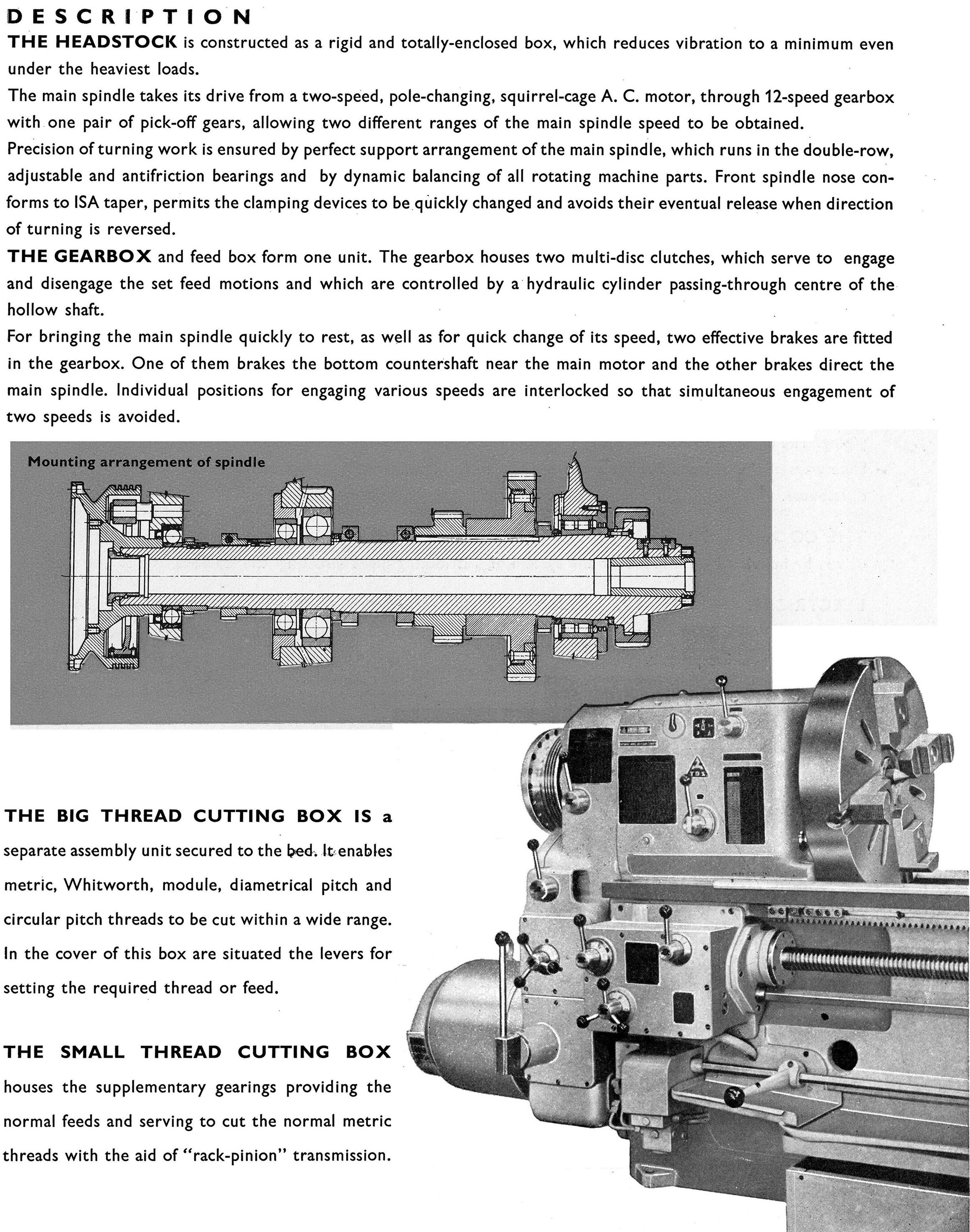 |
|
|
|
|
|
 |
|
|
|
|
|
|
Table at its lowest point. Total vertical travel was 6.6 inches
|
|
|
|
|
|
|
|
 |
|
|
|
|
|
|
Table at its highest point
|
|
|
|
|
|
|
|
|
|
|
|
|
|
 |
|
|
|
|
|
|
The original countershaft survives together with its over-centre, adjustable belt-tension locking mechanism.
|
|
|
|
|
|
|
|
 |
|
|
|
|
|
|
Left and right-handed threaded countershaft belt-tension adjusting block
|
|
|
|
|
|
|
|
 |
|
|
|
|
|
|
Bearings were a shallow taper white metal at the front and, at the rear, a parallel-bore in bronze with a tapered outside with bronze retaining/adjusting nut screwed on its end. Inboard of the front bearing the spindle had what appears to have been a ground-in thread (8 t.p.i. x 1.625 o/d) that drew the spindle into its bearing housing to set the end thrust against the steep taper ground into the outside face of the bore.
|
|
|
|
|
|
|
 |
|
|
|
|
|
|
|
|
|
|
 |
|
|
|
|
|
|
Spindle with retaining nuts, rear bronze bearing and its adjuster nut and the collet draw-tube
|
|
|
|
|
|
|
 |
|
|
|
|
|
|
Front tapered bearing with a steep thrust face at the front - the 8 t.p.i. x 1.625 o/d thread appears to have been ground in
|
|
|
|
|
|
|
 |
|
|
|
|
|
|
Bronze ring used to pull the rear spindle into its housing
|
|
|
|
|
|
|
 |
|
|
|
|
|
|
|
|
|
|
 |
|
|
|
|
|
|
Felt from the top-mounted oiler directed lubricant through a slot cut in the bearings
|
|
|
|
|
|
|
 |
|
|
|
|
|
|
|
|
|
|
|
|
|
|
|
|