 |
 |
 |
 |
 |
 |
 |
 |
 |
 |
 |
 |
 |
 |
 |
 |
 |
 |
 |
 |
 |
 |
 |
 |
 |
 |
 |
 |
 |
 |
 |
 |
 |
 |
 |
 |
 |
 |
 |
 |
|
|
|
|
|
|
|
|
|
|
|
|
|
|
|
|
|
|
|
|
|
|
|
|
|
|
|
|
|
|
|
|
|
|
|
|
|
|
|
|
|
|
|
|
|
|
|
|
|
|
|
An uncommon make - and so seldom discovered - the 14" x 36" (7-inch centre height) Bamford-Chase lathe shown below dates from 1943 and was manufactured by the Bamford-Chase Machine Company, a concern that was active (so it appears) only during the 1940s. Based at 1433 NW Quimby Street in downtown Portland - a town then famous as a shipbuilding centre - Bamford-Chase offered a small range of lathes - all of what which might be classified as lighter industrial type - included both belt-drive and all-geared models. A medium sized, backgeared and screwcutting machine with power sliding and surfacing feeds, the 14-inch was of straightforward design, well made and obviously intended for day-to-day working a repair or engineering shop. However, a clue to the limited number produced may lay in a small detail: instead of engraved or rolled-in digits on the various feed dials, these (and those on the tailstock spindle) were hand stamped. Another pointer to economical production was the similarity in appearance to the Company's 16-inch model with the same size of tailstock, carriage, bed-support plinths and headstock being used - a common trick when building up, as economically as possible, a "range" of lathe of various capacities. Running in Timken taper roller bearings clamped in place by massive 4-bolt caps, the spindle had a 3.5" x 6 t.p.i. threaded nose with a No. 5 Morse taper socket and carried a wide, 3-step cone pulley for drive by a flat belt. Held in the headstock-end support plinth, the countershaft unit was supported on a heavy cast-iron base (hinged for belt tension adjustment), and fitted with plain, white-metal bearings lubricated by pipes connected to outside oil cups; drive came from a remote motor using three V-belts. Driven through an external tumble-reverse assembly, the proper Norton-type, quick-change, twin-tumbler screwcutting and feeds gearbox provided a range of pitches from 2 to 112 t.p.i. - the usual reversible quadrant gear being fitted that gave a choice of coarse or fine feeds by being reversed on its stud. No separate power shaft was fitted, instead the leadscrew was slotted with a key transmitting power to the apron where separate over-centre clutches engaged the sliding and surfacing feeds. Around 94" long, 32" wide and weighing over 3000 lbs this was a strong lathe and originally supplied with a very useful range of equipment that included: faceplates; a taper-turning attachment; thread-dial indicator and an unusual carriage stop that incorporated both 3-position and micrometer types. Also listed by the makers was the usual range of optional equipment: 3 and 4-jaw chucks; Morse centres; fixed and travelling steadies; a tool post grinder; various types of cutting-tool holders and a flat-belt lacing device..
|
|
|
|
|
|
|
|
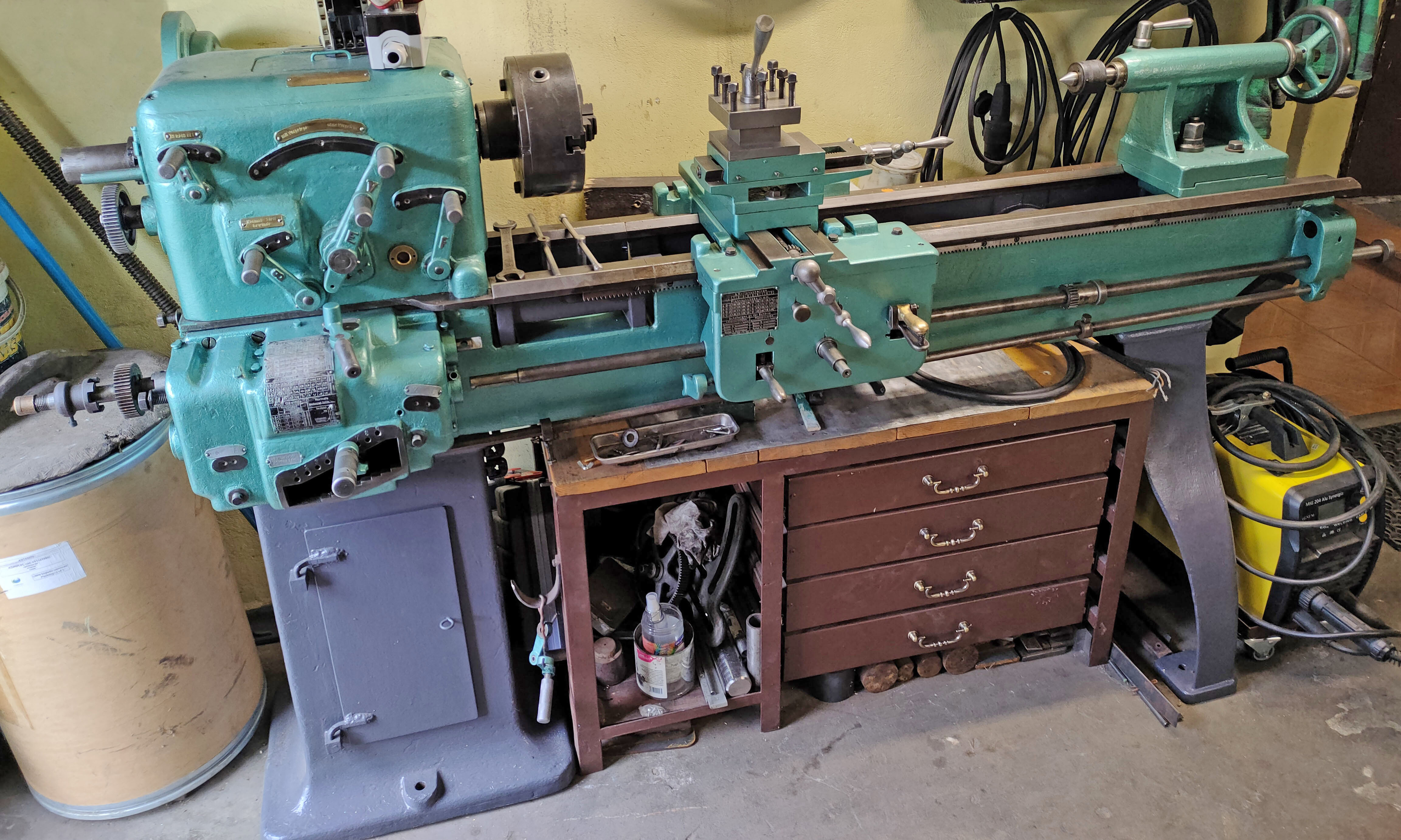 |
|
|
|
|
|
|
Bamford-Chase flat-belt driven 14-inch lathe circa 1943
|
|
|
|
|
|
|
|
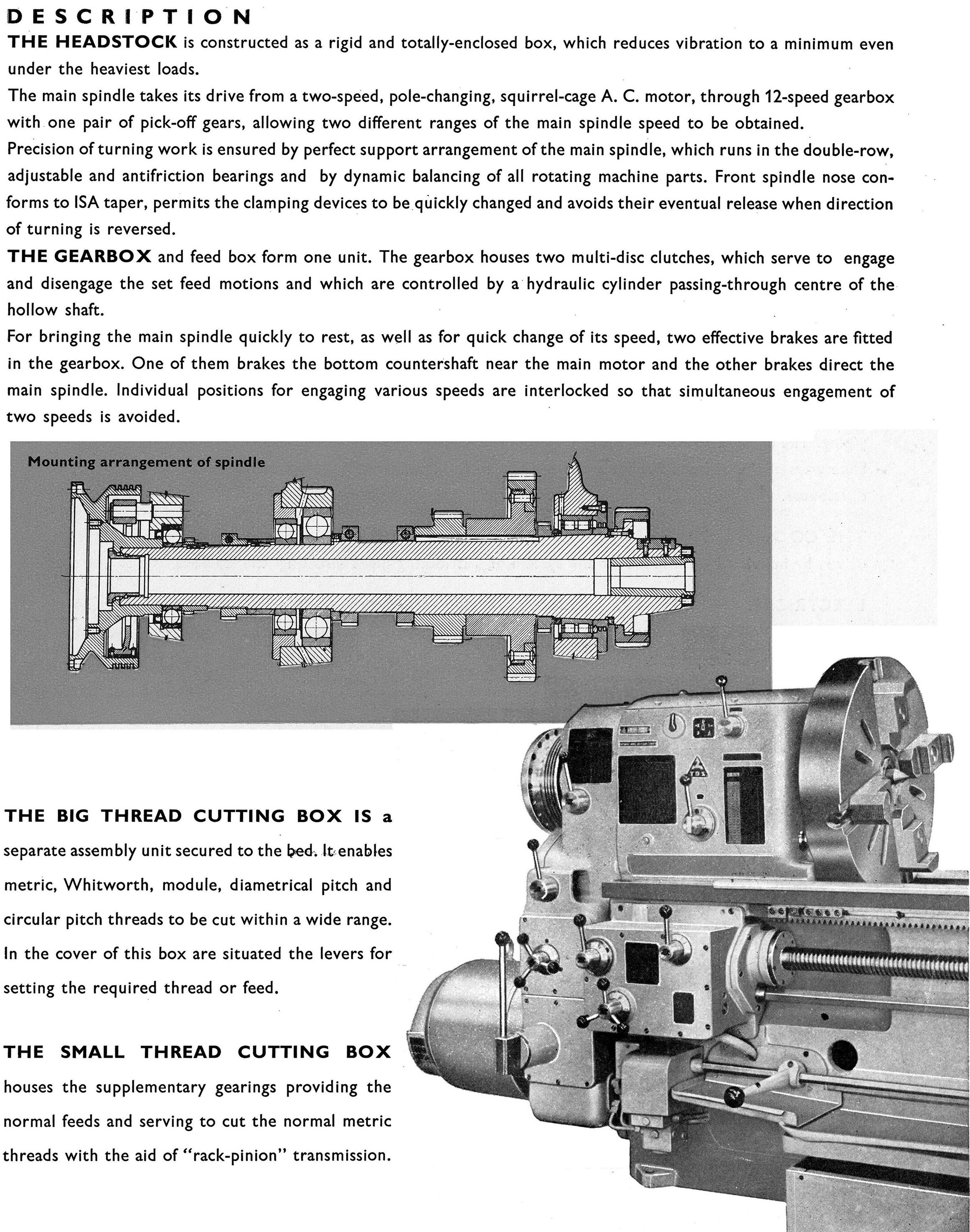 |
|
|
|
|
|
|
Bamford-Chase 18-inch geared-head lathe. Further details can be found at the bottom of the page
|
|
|
|
|
|
|
|
 |
|
|
|
|
|
|
Running in Timken taper roller bearings clamped in place by massive 4-bolt caps, the spindle had a 3.5" x 6 t.p.i. threaded nose with a No. 5 Morse taper socket and carried a wide, 3-step cone pulley for drive by a flat belt.
|
|
|
|
|
|
|
|
|
|
|
|
|
|
 |
|
|
|
|
|
|
Driven through an external tumble-reverse assembly, the proper Norton-type, quick-change, twin-tumbler screwcutting and feeds gearbox provided a range of pitches from 2 to 112 t.p.i. - the usual reversible quadrant gear being fitted that gave a choice of coarse or fine feeds by being reversed on its stud.
|
|
|
|
|
|
|
|
 |
|
|
|
|
|
 |
|
|
|
|
|
|
Running in Timken taper roller bearings clamped in place by massive 4-bolt caps, the spindle had a 3.5" x 6 t.p.i. threaded nose with a No. 5 Morse taper socket and carried a wide, 3-step cone pulley for drive by a flat belt.
|
|
|
|
|
|
|
|
 |
|
|
|
|
|
 |
|
|
|
|
|
 |
|
|
|
|
|
 |
|
|
|
|
|
 |
|
|
|
|
|
 |
|
|
|
|
|
 |
|
|
|
|
|
|
No separate power shaft was fitted, instead the leadscrew was slotted with a key transmitting power to the apron where separate over-centre clutches engaged the sliding and surfacing feeds.
|
|
|
|
|
|
|
|
 |
|
|
|
|
|
|
No separate power shaft was fitted, instead the leadscrew was slotted with a key transmitting power to the apron where separate over-centre clutches engaged the sliding and surfacing feeds.
|
|
|
|
|
|
|
|
 |
|
|
|
|
|
|
Production numbers must have been limited for, instead of engraved or rolled-in digits on the various feed dials, these (and those on the tailstock spindle) were hand stamped.
|
|
|
|
|
|
|
|
 |
|
|
|
|
|
 |
|
|
|
|
|
 |
|
|
|
|
|
 |
|
|
|
|
|
 |
|
|
|
|
|
|
Heavily-built hinged countershaft unit was held in the base of the headstock plinth
|
|
|
|
|
|
|
|
 |
|
|
|
|
|
 |
|
|
|
|
|
|
Each end of the countershaft spindle was fitted with an oil-thrower disc between the nearing halves
|
|
|
|
|
|
|
|
 |
|
|
|
|
An unusual carriage stop that incorporated both 3-position and micrometer types
|
|
|
|
|
|
|
|
 |
|
|
|
|
|
 |
|
|
|
|
|
|
|
|
|
|
|